NISSAN Z32 300ZX Twin Turbo Kit (Part 1)
- Polar Engineering
- Oct 24, 2023
- 7 min read
We’ve all waited long enough!
Introducing Polar Engineering Nissan Z32 300ZX Twin Turbo V-band exhaust manifolds.

Short summary about this project:
After seeing an array of new generation of turbochargers released on the market in the last three years, it was evident that VG30DETT would benefit immensely from all these new releases and is naturally the next step for the Z32 platform. Without delay, I got to work.
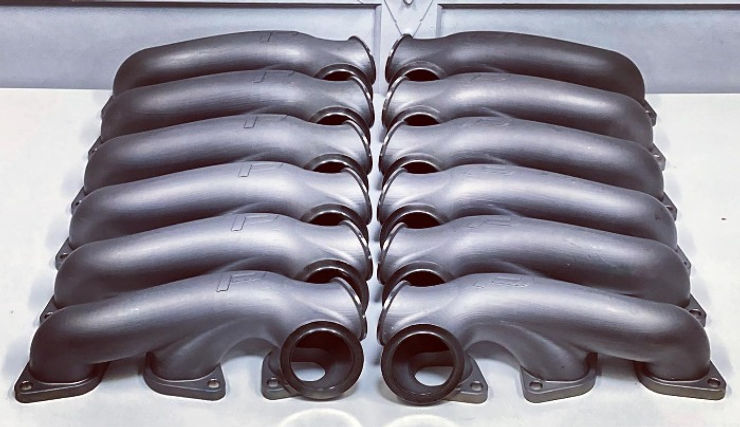
First step was to set specific goals that I wanted to accomplish and work towards them without making any compromises.
My main goals are as follows (not in any order):
-Ability to run a V-band turbine housing
-Ability to run external wastegates
-Retaining all factory amenities that Z32 came with from factory
-Developing new 3” compressor inlet piping and air intake kit
-Developing true 3” downpipes
-Designing symmetrical manifolds to promote even flow on both banks and in all cylinders
-Being able to replicate this kit and have it ready to mass production at reasonable price
-Offer a top tier complete solution to the Z32 enthusiasts all over the world (yes, I thought about the RHD guys too).
-Turbo removal/installation without pulling the engine!
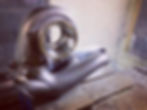
For this project, I decided to stay away from tubular manifolds. That type of manifolds in my (educated) opinion is not a good fit for Z32. They would provide marginal benefits (if any), but would definitely require significant changes to existing systems, giving up amenities and increase cost significantly. If you have any questions about this, please feel free to contact me.
Next, I chose a line of turbochargers that I wanted to build this kit around. It was not difficult to decide on the latest G-series line from Garrett turbochargers. That is by far the best all-around turbocharger line on the market right now. Another perk that stood out with Garrett G series turbos was that they all offered in reverse-rotating configuration which I took advantage of. This kit is able to run G25 and G30 series turbochargers and likely G35 series with slight modifications to power steering hard lines. You should also be able to run Pulsar turbos of same series as a budget option, as well as reverse rotated Tial turbine housings with matching compressor side. Taking into account different ratings and available turbine A/R ratios, I would have over 20 different configurations to choose from.
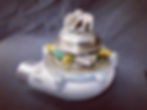
At this point I knew what I wanted to fit in factory Z32 turbocharger locations and that it would require a completely new exhaust manifold to be designed and built. That was where most of the fun (and pain) started for me. I started with two, reverse-rotated G25 turbochargers. It took a significant amount of time to get both turbochargers to sit exactly where I wanted them. It look about five times longer to refine that position to perfection ensuring that they clear all factory accessories including air conditioner and power steering, do not interfere with steering shaft, allow adequate space for running 3” downpipes in the rear and 3” inlet piping in front as well as line up with oil return lines. After that, I did further refining to give some extra space around each turbocharger and have this setup ready to accept G30 line of turbochargers.

After the final manifold outlet positions were confirmed, I designed the manifolds around various constraints that are present on cylinder heads as well as additional goals that I wanted to accomplish. as well.

Let’s briefly talk about these manifolds:
-Manifolds are CAD designed from scratch every step of the way. That allowed me to work around physical dimensions of cylinder head casting and develop free-flowing runners that taper out gradually from each runner inlet all the way towards manifold 3” v-band outlet flange. That greatly helps with exhaust gas reversion and is not possible to do with tubular manifolds. Turbocharger placement also clears factory oil filter trees.
-I was also able to place the wastegate flange in the most favorable location given other physical constraints that I ran into. This kit was designed around Turbosmart 45mm GenV LITE wastegates, but enough room was allocated to run regular, taller Turbosmart 45mm wastegates as well as Tial MV-R and newest Garrett 45mm counterparts.
-Almost perfectly symmetrical manifolds promote even flow through both VG30DETT cylinder heads and individual ports, allow mounting reverse-rotated turbocharger on USDM driver side and eliminating sharp 90-degree elbow off USDM driver side compressor housing. Cylinder #5 and #6 ports will no longer experience flow restrictions that are inherent to previous manifold designs.
-Turbo position clears all parts of factory cylinder head castings with no need of grinding. Compressor inlet piping has been upgraded to 3” diameter and clears low profile engine mounts with no modifications. Inlet piping also clears all factory amenities like power steering pump and AC compressor.
-Physical features: 6mm walls, 12mm flanges, 347 stainless steel casting. Thicker walls were made for superior strength and to allocate extra material in case these manifolds would need to be port matched to custom port sizes on cylinder heads. I would be able to extrude hone these in increments of 0.030” all around. There is plenty of strength and material for all foreseeable performance needs. Once castings are completed, a main face flange would be machined in a single operation as well CNC drilling 6 mounting holes per manifold. Then, the manifold would then be moved on to a 4-axis mill to have two v-band flanges machined into the casting. You read it right, the flanges are machined directly into castings which will eliminate any chance of cracking that happens with weld-on flanges.

Physical constraints are very significant no matter which part of Z32 you are working with. Figuring out perfect position of each turbocharger in the engine bay was less than half the battle and it was definitely the easier half. Next, I needed to route exhaust gasses from each port to an inlet flange of turbine housing in the most efficient, free-flowing and compact manner possible.
It would take lots of pages to go over the details of runner design process, but in this preview post I will only state that there are close to 1000 hours of CAD work, CFD simulation, and flow bench time. I worked closely with a shop that specializes in cylinder head and manifold flow testing. Their experience in this field was of immense help when flow testing the manifolds, mapping flow inside the manifold with a velocity probe, confirming findings when running CFD simulation and using CAD software to fix all problem areas/flow abnormalities. There were 4 total revisions and the last one produced nothing short of fantastic results.

Enough talk, let’s get to some numbers!
Flow testing started with using factory Z32 TT manifolds as a bench mark. Results were very disappointing not only because of low CFM numbers (averaging lower than 140-150CFM per runner) but also because of high deviation between runners. We then moved on to some reputable aftermarket manifolds that are available for Z32 and also their copies. A significant improvement in flow was observed (averaging 210-220CFM per runner). While increased flow is beneficial, these manifolds did not address the issues with high deviation numbers and flow restrictions for cylinder #5 and #6. We also noticed that there was significant turbulence in ports for cylinders #3 and #4. Flow was very unstable. After thorough investigation with a velocity probe, we concluded that merging between long and middle runners was less than optimal. That caused air in runners #3 and #4 to start swirling as it merged with runners from cylinders #1 and #2. I will expand on this in later posts and videos as it deserves thorough coverage. At this point we knew what we were competing against. Polar Engineering ditches factory T25 flange for v-band connection. That gives cross sectional area increase at the flange of around 29% (if I remember correctly). We expected that would be a significant helping factor in chasing high flow numbers. The very first prototype that we tested showed excellent numbers or around 270CFM through runners for cylinders #1/#2 and #5/#6. We were a bit disappointed to find runners for cylinders #3/#4 coming in at around 220CFM. BUT, at this point we knew what was causing these low numbers through center ports! We were not merging the long and middle runners properly. I ran a CFD simulation on all 6 ports and we confirmed digital data by comparing it to physical data that we collected with a velocity probe. After significant modifications to long runner routing and internal runner structure, CFD simulation looked much better. Flow bench results confirmed that the issue was addressed and resolved!
Final flow numbers were:
Polar Engineering manifold
73*F, 30.06 baro, 39%Hum Ambient
Tested @ -28"wc applied to manifold collector
Manifold runner inlet radius 9mm
Cal plate 232.1, reading 230
Cal plate 287.4 reading 288
CFM readings are not adjusted for ambient air density
----------------- Gasket centered
Short---------------------257
Middle-------------------252
Long----------------------258
Note: all testing was done with factory gasket in place and centered. This was done as a benchmark of port size that was also used by others when testing Z32 manifolds. I wanted to let you compare apples to apples when looking at data that others have gathered and recorded in the past.

Couple of things to note here… Since I am using reverse-rotated turbos, I was able to make mirrored manifolds which means that runners #1 and #2 flow exactly the same (as well as 3&4 and 5&6). The deviation in flow numbers is borderline negligible. This would not be possible without proper CFD analysis and tuning (in CAD software) the way that long/middle runners merge. Last, but certainly not least, we were able to provide unobstructed path for gasses exiting ports #5 and #6. This is the first manifold that does that!
Now that I had digital designs of these manifolds, it was time to have them cast. I set some goals here as well:
- Manifolds have to be investment cast to achieve required dimensional accuracy and details
-Alloy of choice would have to be 347 stainless steel, which has superior characteristics for this application.
-100% made in the USA, yes 100% USA made!

Making no compromises, I received the first two sets of my cast 347 stainless steel manifolds and verified dimensional accuracy of these casting. The foundry absolutely knocked it out of the park with tooling, mold production and casting process. Shrinkage calculations were dead on and I honestly could not believe how dimensionally correct these came out!
These will be priced fair (just like all my other parts), but they will not be cheap. Please understand that I put in many times more work than goes into similar manifolds that are available on the market for other platforms. I can also tell you that this kit will be one of the few that is 100% made in the USA. For that reason, please expect market pricing before you reach out to express interest.
Once again, I appreciate everyone’s support and look forward to providing everyone with an off the shelf option to run the most modern turbochargers available on the market.
Thank you!